The OMAX 120X Abrasive Water Jet is a powerful and versatile tool that stands out in the world of precision cutting. Designed to handle a variety of materials with ease, this machine is an excellent choice for industries that require high precision, flexibility, and efficiency.
Whether you are involved in the manufacturing, aerospace, or automotive sectors, the OMAX 120X promises to deliver outstanding performance. This review delves into the key features, advantages, and potential drawbacks of this impressive water jet-cutting system.
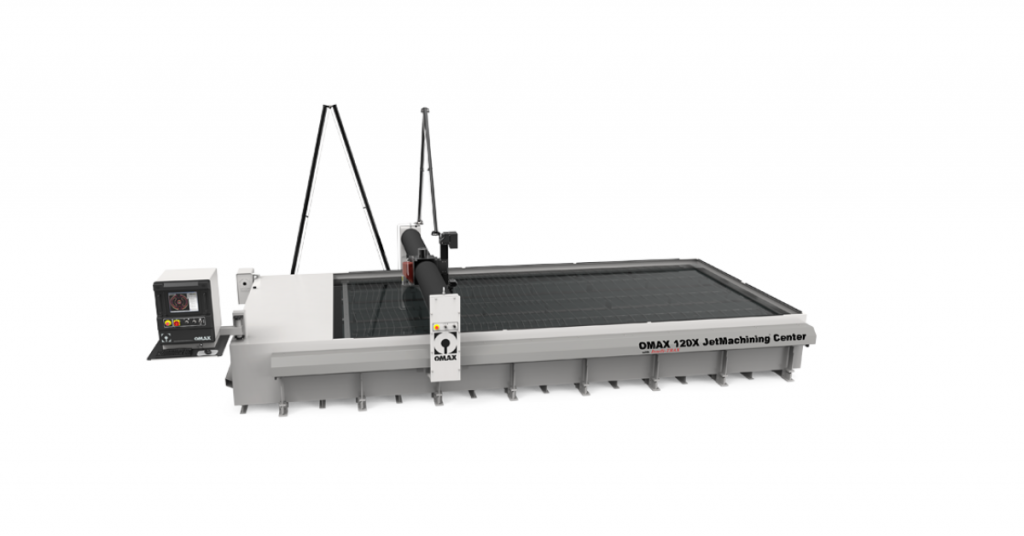
Key Features of the OMAX 120X Abrasive Water Jet
- High Precision Cutting: Delivers accurate cuts with smooth edges, reducing the need for secondary finishing.
- Versatile Material Handling: Cuts through a wide range of materials, including metals, composites, glass, and ceramics.
- Large Cutting Area: Offers a 10 feet by 20 feet cutting space, ideal for large projects and multiple small parts.
- Advanced Software Integration: Intelli-MAX software provides easy-to-use controls, CAD file import, and optimized cutting paths.
- Efficient Pump System: Features a direct drive pump that operates at lower RPM for reduced wear, lower maintenance, and energy efficiency.
Pros and Cons of the OMAX 120X Abrasive Water Jet
Pros:
- High Precision: Delivers accurate, smooth cuts, reducing the need for secondary processing.
- Versatile Material Handling: Cuts through various materials including metals, glass, and composites.
- Large Cutting Area: Accommodates large projects and multiple smaller parts simultaneously.
- User-Friendly Software: Intelli-MAX software offers easy controls and optimized cutting paths.
- Efficient Pump System: Reduces wear, maintenance costs, and energy consumption.
Cons:
- High Initial Investment: The upfront cost is significant, which may be a barrier for smaller businesses.
- Space Requirements: Requires a substantial amount of space, which might be a limitation for smaller workshops.
Key Features
Precision Cutting
One of the standout features of the OMAX 120X is its ability to deliver precision cutting. The machine utilizes a high-pressure stream of water mixed with abrasive particles to cut through materials with incredible accuracy. This process allows for intricate designs and shapes to be cut without the need for secondary finishing, saving time and reducing material waste. The precision is further enhanced by OMAX’s Intelli-MAX software, which optimizes the cutting paths for maximum efficiency and accuracy.
Versatile Material Handling
The OMAX 120X is renowned for its versatility in handling a wide range of materials. From metals and composites to glass and ceramics, this water jet can cut through almost anything. This versatility makes it an invaluable asset in various industries where different materials are used. Whether you need to cut thick steel plates or delicate glass, the OMAX 120X can handle the task with ease.
Large Cutting Area
With a cutting area of 10 feet by 20 feet, the OMAX 120X provides ample space for large projects. This large working area allows for the processing of large sheets of material, reducing the need for multiple setups and increasing overall efficiency. The substantial cutting area also means that multiple smaller parts can be cut simultaneously, further improving productivity.
Advanced Software Integration
The OMAX 120X is equipped with the Intelli-MAX software suite, which is known for its user-friendly interface and powerful features. The software allows users to import CAD files directly, generate precise cutting paths, and control the machine with ease. The Intelli-MAX software also includes features like taper compensation and collision sensing, which enhance the cutting quality and protect the machine from damage.
Efficient Pump System
The machine features a highly efficient direct drive pump system that operates at a lower RPM compared to traditional intensifier pumps. This design reduces wear and tear, leading to longer pump life and lower maintenance costs. The efficient pump system also contributes to the overall energy efficiency of the machine, reducing operating costs.
Eco-Friendly Operation
Water jet cutting is inherently more environmentally friendly compared to other cutting methods, such as laser or plasma cutting. The OMAX 120X does not produce hazardous fumes or thermal distortion, making it a safer and cleaner option for operators and the environment. Additionally, the abrasive materials used in the cutting process can often be recycled, further reducing the environmental impact.
Advantages
High Precision and Quality
The OMAX 120X excels in delivering high-precision cuts with smooth edges, reducing the need for secondary finishing processes. This high level of precision ensures that parts fit together perfectly, which is crucial in industries like aerospace and automotive where accuracy is paramount.
Cost-Effective Operation
Despite the initial investment, the OMAX 120X proves to be cost-effective in the long run. The efficient pump system, reduced maintenance requirements, and the ability to minimize material waste all contribute to lower operating costs. Additionally, the machine’s versatility means that it can replace several different cutting tools, further enhancing its cost-effectiveness.
Enhanced Productivity
The combination of a large cutting area, advanced software, and the ability to cut a variety of materials results in enhanced productivity. The OMAX 120X can handle complex projects with ease, allowing businesses to take on more work and complete it faster. This increase in productivity can lead to higher revenues and improved profitability.
Potential Drawbacks
Initial Investment
One of the primary drawbacks of the OMAX 120X is its initial cost. As a high-end piece of equipment, the upfront investment can be significant. However, for businesses that require high precision and versatility, the long-term benefits and cost savings often justify the initial expense.
Space Requirements
The OMAX 120X requires a substantial amount of space due to its large cutting area. Businesses need to ensure they have adequate space to accommodate the machine and its associated components. This space requirement can be a limitation for smaller workshops or facilities with limited floor space.
Learning Curve
While the Intelli-MAX software is user-friendly, there is still a learning curve associated with operating the OMAX 120X. Operators need to be trained to fully utilize the machine’s capabilities and to maintain it properly. This training period can temporarily impact productivity as staff become proficient with the new equipment.
Cutting Speed and Efficiency
One of the remarkable features of the OMAX 120X Abrasive Water Jet is its impressive cutting speed. The combination of high-pressure water and abrasive particles allows the machine to cut through materials at a rapid pace without compromising precision. This efficiency is particularly beneficial for high-volume production environments where time is of the essence. The fast cutting speeds reduce the overall project time, allowing businesses to meet tight deadlines and increase their throughput.
Customization and Flexibility
The OMAX 120X offers a high degree of customization and flexibility, making it suitable for a wide range of applications. The machine can be easily adjusted to accommodate different cutting needs, from intricate designs to straightforward cuts. Users can modify the cutting parameters such as pressure, abrasive flow rate, and cutting speed to achieve the desired results. This flexibility ensures that the OMAX 120X can handle diverse projects, providing a one-stop solution for various cutting requirements.
Durability and Build Quality
Constructed with robust materials and designed for heavy-duty use, the OMAX 120X is built to last. The machine’s frame and components are engineered to withstand the rigors of industrial use, ensuring long-term reliability and minimal downtime. The durable build quality reduces the frequency of repairs and replacements, leading to lower maintenance costs and extended machine life. This durability is a testament to OMAX’s commitment to quality and excellence in manufacturing.
User Experience and Interface
The user experience with the OMAX 120X is enhanced by its intuitive interface and easy-to-use controls. The Intelli-MAX software provides a straightforward and user-friendly platform for operators to manage the cutting process. The software includes comprehensive tutorials and support features, making it accessible even for those new to water jet cutting technology. The touch-screen interface and streamlined controls allow operators to quickly set up and execute cutting tasks, improving overall efficiency and reducing the learning curve.
Applications and Industry Use
Aerospace Industry
In the aerospace industry, precision and quality are critical. The OMAX 120X is particularly well-suited for this sector due to its ability to produce intricate and accurate cuts on materials like titanium, aluminum, and composites. The machine’s precision ensures that components meet stringent industry standards, reducing the risk of defects and improving the safety and performance of aerospace products.
Automotive Industry
The automotive industry benefits greatly from the OMAX 120X’s capabilities. The machine can efficiently cut complex shapes and designs required for automotive parts, from body panels to engine components. The high cutting speed and precision help manufacturers meet the high demands of the industry while maintaining quality and reducing production costs.
Manufacturing and Fabrication
For general manufacturing and fabrication, the OMAX 120X offers unparalleled versatility. It can cut through various materials, including metals, plastics, and composites, making it a valuable tool for custom fabrication projects. The ability to produce high-precision parts with smooth edges eliminates the need for secondary processes, streamlining production and reducing costs.
Art and Design
Artists and designers also find the OMAX 120X to be an invaluable tool. The machine’s precision and ability to cut intricate patterns allow for the creation of detailed and complex designs in various materials, including glass, stone, and metal. This capability opens up new possibilities for artistic expression and innovative design solutions.
Maintenance and Support
Regular Maintenance
To ensure optimal performance and longevity, the OMAX 120X requires regular maintenance. This includes routine checks of the pump system, abrasive delivery system, and cutting head. The machine’s design makes maintenance tasks straightforward, with easily accessible components and clear instructions provided in the user manual. Regular maintenance not only keeps the machine running smoothly but also prevents unexpected downtime and costly repairs.
Technical Support and Training
OMAX provides comprehensive technical support and training for the 120X Abrasive Water Jet. The company offers detailed training programs for operators, covering everything from basic operations to advanced cutting techniques. Additionally, OMAX’s technical support team is readily available to assist with any issues or questions, ensuring that users can maximize the machine’s potential. This support network is a valuable resource for businesses, helping them to maintain high productivity and efficiency.
Innovations and Technology
Intelli-VISOR System Monitoring
The OMAX 120X is equipped with the Intelli-VISOR System Monitoring, a cutting-edge technology that provides real-time monitoring of the machine’s performance. This system tracks various parameters, such as pump pressure, abrasive flow rate, and nozzle condition, alerting operators to any issues that may arise. The Intelli-VISOR system helps to prevent problems before they occur, ensuring consistent performance and reducing downtime.
A-Jet Articulating Cutting Head
The A-Jet articulating cutting head is an optional feature that adds even more versatility to the OMAX 120X. This cutting head can be angled to produce beveled edges and complex geometries, expanding the range of possible applications. The A-Jet is particularly useful for creating parts that require precise angles and complex shapes, making it an excellent addition for advanced cutting tasks.
Conclusion
The OMAX 120X Abrasive Water Jet is a top-tier cutting machine that offers unmatched precision, versatility, and efficiency. Its ability to handle a wide range of materials and large-scale projects makes it an essential tool for various industries. The advanced features, durable construction, and user-friendly interface ensure that the OMAX 120X delivers consistent, high-quality results.
While the initial investment and space requirements may pose challenges, the long-term benefits of enhanced productivity, cost savings, and superior performance make the OMAX 120X a worthwhile investment. For businesses seeking a reliable and powerful cutting solution, the OMAX 120X stands out as a premier choice, capable of meeting the most demanding cutting needs with precision and ease.
Frequently Asked Questions About the OMAX 120X Abrasive Water Jet
What materials can the OMAX 120X cut?
- The OMAX 120X can cut a wide range of materials, including metals, composites, glass, and ceramics.
How large is the cutting area?
- The cutting area of the OMAX 120X is 10 feet by 20 feet.
Is the software difficult to use?
- The Intelli-MAX software is user-friendly and provides easy controls and optimized cutting paths.
What are the maintenance requirements?
- Regular maintenance includes checking the pump system, abrasive delivery system, and cutting head to ensure optimal performance.
How efficient is the pump system?
- The direct drive pump system operates at a lower RPM, reducing wear, maintenance costs, and energy consumption.
Related Searches/Variations of the OMAX 120X Abrasive Water Jet
- OMAX 120X Water Jet Cutter
- OMAX 120X High-Precision Water Jet
- OMAX 120X Large Cutting Area Water Jet
- OMAX 120X Versatile Material Cutting
- OMAX 120X Intelli-MAX Software Water Jet